Definition of a Quality Specialist
A Quality Specialist is a professional guardian of excellence, playing a pivotal role in ensuring that products, services, and processes meet established standards and customer expectations. They are the meticulous overseers who scrutinize every detail, applying rigorous testing and assessment methods to uphold the integrity of an organization's output. With a keen eye for both compliance and improvement, Quality Specialists serve as the critical link between the theoretical frameworks of quality management and their practical application in the workplace. Their expertise not only safeguards a company's reputation but also fosters a culture of continuous enhancement, making them indispensable in industries where precision and reliability are paramount.
What does a Quality Specialist do?
Quality Specialists are the guardians of product and service excellence, meticulously overseeing every aspect of an organization's output to ensure it meets established standards and customer expectations. They employ a variety of tools and methodologies to monitor, analyze, and improve the quality of processes and products, often working cross-functionally to instill a culture of continuous improvement. Their role is critical in minimizing defects, maintaining compliance with regulations, and enhancing customer satisfaction and loyalty.
Key Responsibilities of a Quality Specialist
Developing and implementing quality management systems and procedures to ensure consistent product or service quality
Conducting regular inspections and audits to ensure adherence to industry standards and regulatory requirements
Analyzing quality data and metrics to identify trends and areas for improvement
Collaborating with cross-functional teams to establish quality requirements for raw materials, components, products, and processes
Leading root cause analysis and implementing corrective actions to address quality issues
Training and guiding team members on quality control processes and best practices
Managing the non-conformance and corrective action processes, including documentation and reporting
Facilitating continuous improvement initiatives and promoting a culture of quality throughout the organization
Participating in product development projects to ensure quality considerations are integrated from the outset
Coordinating with suppliers and vendors to ensure their products and services meet quality standards
Preparing and presenting reports on quality performance to management and stakeholders
Keeping abreast of new quality standards, technologies, and industry developments to maintain professional expertise
Day to Day Activities for Quality Specialist at Different Levels
The day-to-day responsibilities of a Quality Specialist can differ greatly depending on their level of experience within the field. Those who are new to the role may find themselves focusing on learning industry standards and compliance requirements, while mid-level Quality Specialists often take on more responsibility in implementing quality control processes. At the senior level, Quality Specialists are expected to lead quality assurance strategies and may influence organizational policies. Each career stage brings a unique set of tasks and objectives that contribute to the overall goal of maintaining and improving product or service quality.
Daily Responsibilities for Entry-Level Quality Specialists
At the entry level, Quality Specialists are typically learning the foundational elements of quality assurance and control. Their daily activities are centered around supporting the quality team and gaining an understanding of the quality standards relevant to their industry.
Assisting with the development and implementation of quality control inspections
Documenting quality issues and compiling data for quality reports
Participating in internal audits and compliance checks
Collaborating with team members to resolve minor quality problems
Learning about industry-specific regulations and quality standards
Engaging in training programs to enhance quality-related skills and knowledge
Daily Responsibilities for Mid-Level Quality Specialists
Mid-level Quality Specialists are more involved in the active management of quality control processes and have a greater impact on the outcomes. They are responsible for identifying issues, suggesting improvements, and ensuring that products or services meet quality standards.
Conducting detailed data analysis to identify trends in quality issues
Leading root cause analysis and implementing corrective actions
Managing specific quality control projects and initiatives
Training and guiding junior Quality Specialists and other staff
Collaborating with cross-functional teams to integrate quality practices
Reviewing and updating quality procedures and documentation
Daily Responsibilities for Senior Quality Specialists
Senior Quality Specialists are leaders in the quality domain, responsible for strategic planning and decision-making. They play a crucial role in shaping the quality culture of an organization and ensuring compliance with the highest standards.
Developing and overseeing the implementation of quality assurance strategies
Managing and mentoring a team of Quality Specialists and quality-focused staff
Leading organizational preparations for external audits and certifications
Advising on quality improvements and best practices at the management level
Establishing key performance indicators and metrics for quality assessment
Driving continuous improvement initiatives and fostering a quality-centric environment
Types of Quality Specialists
Quality assurance is a critical component of any industry that values consistency, safety, and customer satisfaction. Within this broad field, Quality Specialists play a pivotal role in maintaining and improving product and service standards. These professionals come from diverse backgrounds and specialize in various aspects of quality, each bringing a unique set of skills and focus areas to their roles. Their specializations reflect the diverse needs of different sectors and the varied approaches to managing and ensuring quality. From manufacturing to software development, each type of Quality Specialist contributes to the overarching goal of delivering excellence.
Manufacturing Quality Specialist
Manufacturing Quality Specialists are deeply embedded in the production process, focusing on the consistency and reliability of physical products. They have a keen eye for detail and are often involved in developing and implementing quality control procedures, inspecting products at various stages of production, and ensuring compliance with industry standards and regulations. Their technical expertise allows them to identify defects and work with production teams to rectify issues, minimizing waste and ensuring that the final products meet the required specifications. This role is crucial in industries such as automotive, aerospace, consumer goods, and pharmaceuticals, where product integrity is paramount.
Software Quality Assurance (SQA) Specialist
Software Quality Assurance Specialists concentrate on the quality of software development and deployment. They possess a strong understanding of software development life cycles and methodologies, such as Agile or Waterfall. SQA Specialists design and execute test plans, report bugs, and collaborate with developers to ensure that software is functional, reliable, and user-friendly. They play a vital role in tech companies or any business that relies on software for operations, ensuring that applications perform as intended before reaching the end-user.
Food Safety Quality Specialist
Food Safety Quality Specialists are experts in the standards and regulations that govern the food and beverage industry. Their work is essential to prevent foodborne illnesses and ensure that products are safe for consumption. They conduct hazard analyses, develop critical control plans, and oversee compliance with local and international food safety standards, such as HACCP and FDA regulations. These specialists work closely with supply chains, production teams, and regulatory bodies, making their role indispensable in maintaining public health and trust in food brands.
Quality Systems Specialist
Quality Systems Specialists focus on the design, implementation, and maintenance of an organization's quality management system (QMS). They are well-versed in quality standards such as ISO 9001 and are responsible for ensuring that all processes within an organization meet these standards. Their role involves conducting internal audits, facilitating external audits, and leading continuous improvement initiatives. By maintaining a robust QMS, these specialists help organizations achieve consistency in their operations and align with best practices, which is vital for customer satisfaction and competitive advantage.
Regulatory Affairs Quality Specialist
Regulatory Affairs Quality Specialists specialize in navigating the complex landscape of industry regulations and ensuring that products comply with all legal requirements. They are knowledgeable about the regulatory environment of their specific industry, whether it be pharmaceuticals, medical devices, chemicals, or any other sector subject to stringent regulatory oversight. These specialists work on product registrations, submissions, and liaise with regulatory agencies to facilitate market access for new products. Their expertise is critical for companies that must adhere to regulatory standards to bring their products to market legally and ethically.
Quality Improvement Specialist
Quality Improvement Specialists are dedicated to enhancing processes and outcomes within an organization. They use data-driven approaches, such as Six Sigma or Lean methodologies, to identify areas for improvement and implement changes that lead to higher efficiency and better quality. These specialists often work in healthcare, manufacturing, or service industries, where they can make a significant impact on operational excellence and customer satisfaction. Their ability to analyze performance metrics, manage cross-functional teams, and drive change initiatives makes them key players in an organization's continuous improvement culture.
What's it like to be a Quality Specialist?
Ted Lasso
Product Manager Company
"Being a product manager is a lot like doing XYZ...you always have to XYZ"

Ted Lasso
Product Manager Company
"Being a product manager is a lot like doing XYZ...you always have to XYZ"

Stepping into the role of a Quality Specialist means entering a world where precision and continuous improvement are at the forefront. This position is the backbone of ensuring that products and services meet established standards and exceed customer expectations. As a Quality Specialist, you are the gatekeeper of excellence, meticulously analyzing processes, identifying defects, and implementing solutions to enhance overall quality.
In this role, every day involves a rigorous examination of workflows, collaboration with production teams, and a relentless pursuit of eliminating inefficiencies. It's a career characterized by attention to detail - one where analytical skills and a methodical approach are essential, and where your contributions are integral to the reputation and reliability of your company's offerings. For those drawn to a career that emphasizes quality, precision, and has a direct impact on customer satisfaction, being a Quality Specialist offers a rewarding and impactful path.
Quality Specialist Work Environment
The work environment for Quality Specialists can vary greatly depending on the industry and company size. Typically, it's a structured and process-oriented setting where meticulousness and consistency are paramount. Quality Specialists may work in manufacturing plants, laboratories, corporate offices, or healthcare facilities, often in environments that are designed to minimize errors and promote high standards. The role may involve a combination of on-the-floor inspections, data analysis, and meetings with management and production teams to discuss quality improvements.
Quality Specialist Working Conditions
Quality Specialists generally work full-time, with the possibility of overtime during critical production periods or when major quality issues arise. They spend a significant amount of time reviewing processes, conducting tests, and documenting results. The job requires a keen eye for detail and the ability to remain focused on tasks for extended periods. While the work can be repetitive, it is also critical, as maintaining high-quality standards is essential for the success and reputation of the business. The conditions can be demanding, but the satisfaction of ensuring excellence makes the role gratifying.
How Hard is it to be a Quality Specialist?
The role of a Quality Specialist can be challenging due to the high level of attention and precision required. The difficulty often lies in the need to maintain unwavering focus on quality standards while managing the pressures of production timelines and cost constraints. Quality Specialists must possess a strong understanding of quality control methodologies, statistical analysis, and, in some cases, regulatory compliance. They must be effective communicators to convey findings and persuade others to implement changes.
The job can be fast-paced, especially in industries with rapid production cycles, and Quality Specialists must be able to quickly identify and address quality issues. Despite these challenges, many Quality Specialists find the role satisfying as they play a crucial part in ensuring that customers receive the best possible products and services. It's a career well-suited to those who take pride in their work, are detail-oriented, and are passionate about upholding standards of excellence.
Is a Quality Specialist a Good Career Path?
Being a Quality Specialist is a solid career choice for those interested in a detailed-oriented and process-driven profession. The demand for Quality Specialists remains steady, as organizations across various sectors strive to maintain high standards and competitive edges in their markets. Quality Specialists often enjoy competitive salaries, opportunities for career advancement, and the chance to work in diverse industries, from manufacturing to healthcare to technology.
The role offers a clear path for professional development, with potential to move into senior quality management positions or specialize in areas such as Six Sigma or Lean methodologies. With a focus on continuous improvement and operational excellence, the career of a Quality Specialist is both stable and filled with opportunities for those who are committed to quality and have a keen eye for detail.
FAQs about Quality Specialists
How do Quality Specialists collaborate with other teams within a company?
Quality Specialists are integral to fostering cross-departmental synergy, ensuring product standards align with regulatory compliance and customer expectations. They work closely with R&D for quality design, manufacturing to monitor processes, and supply chain to audit materials. They also engage with customer service to address quality concerns and feedback, facilitating continuous improvement. This collaboration is pivotal for maintaining the integrity of the company's offerings and upholding its reputation for excellence.
What are some common challenges faced by Quality Specialists?
Quality Specialists grapple with ensuring compliance amidst ever-evolving regulatory standards, which requires constant vigilance and adaptability. They face the challenge of maintaining high-quality levels while balancing cost-efficiency, often under tight deadlines. Moreover, they must effectively communicate the importance of quality processes across departments, fostering a culture of continuous improvement. Navigating the complexities of data analysis to identify trends and root causes of quality issues also demands a high level of expertise and critical thinking.
What does the typical career progression look like for Quality Specialists?
Quality Specialists typically begin their careers mastering the fundamentals of quality assurance, focusing on compliance, and process improvement. With experience, they may progress to Senior Quality Specialists, taking on more responsibility for developing quality standards and leading audit teams. Advancement can lead to Quality Manager roles, overseeing entire quality systems and departments. Further growth may involve strategic positions such as Director of Quality, where they shape quality policies and culture across the organization. Ultimately, they could reach executive levels like VP of Quality, driving company-wide excellence. The path from hands-on quality control to strategic leadership varies by individual achievement and organizational needs.
Up Next
How To Become a Quality Specialist in 2024
Learn what it takes to become a JOB in 2024
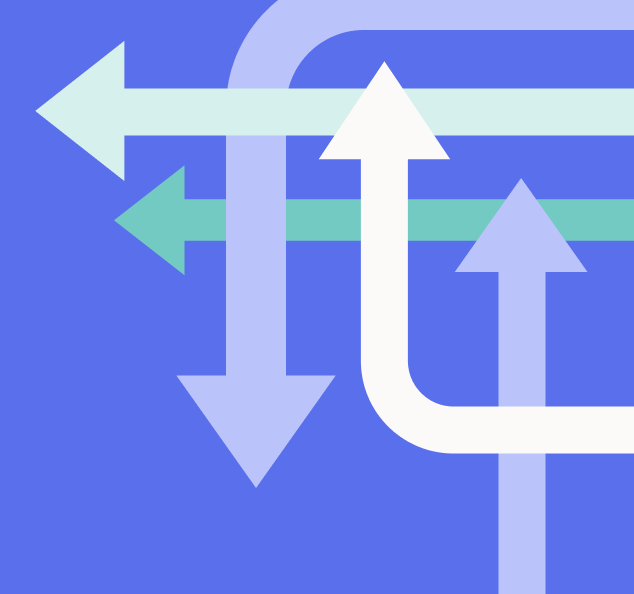